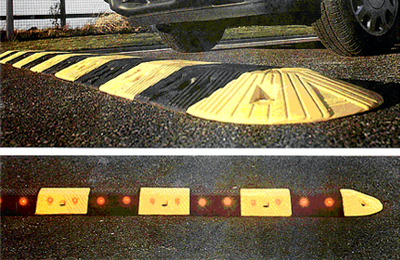
Sleeping Policeman (Road humps / Speed bumps)
The most effective measures to lower vehicle speed is by using
sleeping policeman or known as road hump. The road humps are designed
to have different sizes and shape to suit the requirements and place
of services. Some are narrow as to deliver a sharp jolt to vehicle
suspension and to gives discomfort when crossing at high speed. The
wide humps are mainly for further reducing the vehicle speed due
to longer crossing time. The road hump is normally extended from
curb to curb across the full road with a drainage gap.
They are made of a hard, high impact rubber that lasts longer
than plastic, asphalt or concrete speed bumps. They are moveable
can be easily relocated. Road hump is grooved to provide traction
in rain or snow and easy drainage of water. Built-in cats’ eyes
provide necessary night visibility, alerting drivers to slow down.
The road hump is made from NR and SR and its blend.
The black slab is made from black rubber compound base on 100% NR.
The rubber is formulated with suitable hardness to with stand heavy
load, forces and compression. The tear and tensile strength is immaculately
high so that it resistant to tearing and chunking. The vulcanisate
is also designed to be weather resistance by adding antiozonant and
antioxidant.
For yellow compound similar properties were assured but with extra
protection on weathering. Since coloured compound more prone to
weathering it is formulated base on blending with weather resistant
rubber. The colour pigment used is also of higher grade with weather
fastness above approximately 5. Extra protection agents were added
into the formulation such as UV absorber and light stabilizer.
With these extra protections the yellow slab or portion of the
hump should be more resistance to fading and weathering.
The road hump is also designed to have built in reflector. The
reflector used is of high intensity grade which is bright, durable,
retroreflective material designed to have similar appearance when
viewed in the daylight or by retroreflected light at night. The
reflective sheeting consists of optical lens elements adhered to
a synthetic resin and encapsulated by a flexible, transparent plastic
with a smooth outer surface. The reflector sheeting featured a
pressure-sensitive adhesive for ease of application. The main properties
of it performance are 3 times brighter than Engineer Grade reflective
sheeting and retain good reflective to ensure safety condition.
Manufacturing Process
- Mixing of compound
There are two compounds used in the manufacturing of road hump,
one black and one yellow. The compounds are mixed separately either
using internal mixer or two-roll mill. If internal mixer is to
be used, master batch is mixed in the internal mixer first under
controlled temperature. The master batch is then added with curatives
using two-roll mill. If the mixing is to be carried out on two-roll
mill, the mixing is to begin with mastication of the rubber and
followed by addition of ingredients such as activators, filler
and oil. The curatives are to be added last.
- Curing of components
There are three separate components for making road hump, they
are black and yellow intermediate slabs and the end slab. The
intermediate slabs using the same mould for black and yellow.
However the mould must be cleaned before changing to new compound.
The curing can be carried out using the same press for each individual
component. The economical moulding temperature is 170°C. The
cure time is approximately 30 minutes for intermediate slab and
approximately 20 minutes for end slab. The moulds are designed
to facilitate easy fixing to the platens.
- Trimming process
- Bolting to road surfaces
|